About Waterjet
Waterjet: Cutting with Liquid Force™ Tool
The power of ultrahigh-pressure water is remarkable. From cutting to cleaning, the shear strength of water is not only unexpected, but astounding. Waterjet is the material processing solution of the future. Learn more here.
Benefits of Waterjet
Powerful
Waterjet can cut the hardest materials in just one pass, including stainless steels, super alloys (such as Titanium, Inconel and more) and advanced composites, up to 300 mm. For other applications, ultrahigh-pressure waterjet performs as an extremely powerful pressure washer: it can remove paint on large steel structure (oil tanks, ship hauls,…), ceramic shells on investment castings, breakable burrs on machined parts or tough coatings such as Thermal Barrier Coatings (TBC), abradable and wear resistant coatings on turbine parts.
Versatile
Liquid Force™ power can be applied virtually on any material. Depending on the application, setup time can be as quick as few clicks of mouse. For thick or thin materials, from rough cutting to high precision parts, from paint to thermal barrier coatings, from ceramic shell to metallic burrs, waterjet is the most versatile industrial solution.
Natural
Waterjet is a very gentle manufacturing process. Consisting of predominately pressurized water, and sometimes mixed with natural abrasive sand when cutting hard materials. It is a cold process: no heat affected zone (HAZ) on the parts and no hazardous gases are generated. No harmful or noxious chemicals are used. In addition, process water can be used in closed-loop to minimize water consumption and effluents going to drain.
Flexible
“If you can draw it, waterjet can cut it!”: this moto is a perfect summary for the flexibility of waterjet. For other applications, flexibility to apply Liquid Force™ to complex parts solves many advanced manufacturing challenges with a repeatable tool delivering consistent quality; your tool is always sharp!
In addition, water being a soft tool, very little force or stress apply on the material: your part’s geometry and integrity are preserved and fixturing can be very light, and therefore cost effective.
The Science Behind the Waterjet Process
Ultrahigh-pressure processes can operate between 1,000 bar / 15,000 psi and 10,000 bar / 150,000 psi. As a comparison, a pressure washer operates around 100 bar / 1,500 psi. At these levels of pressure, water becomes compressible and this volume compressibility is the key for understanding the incredible power of waterjets. Here’s how the technology works:
1
Pressure is generated in a specially designed pump. Two pump technologies are available: intensifier pumps using the surface ratio between a piston and a plunger; and direct drive pumps working somewhat like a car engine.
2
Pressurized water is transported from the pump to the head through specific flexible hoses or stainless-steel tubing.
3
In the head, pressure is converted to velocity through a tiny jewel orifice, traditionally ruby, sapphire or diamond. The orifice generates a supersonic waterjet stream with a diameter usually between 0.5 and 1.5 mm travelling between 2 and 4 times the speed of sound.
4
For toughest operations, including cutting hard materials such metals, a second stage is added. The supersonic jet is travelling through this stage, creates a venturi effect to mix abrasive sand. The sand is accelerated by the water, creating a highly powerful supersonic particle stream erosion (PASER® is the first patent for an abrasive waterjet cutting head in the early 80’s)
1
Pressure is generated in a specially designed pump. Two pump technologies are available: intensifier pumps using the surface ratio between a piston and a plunger; and direct drive pumps working somewhat like a car engine.
2
Pressurized water is transported from the pump to the head through specific flexible hoses or stainless-steel tubing.
3
In the head, pressure is converted to velocity through a tiny jewel orifice, traditionally ruby, sapphire or diamond. The orifice generates a supersonic waterjet stream with a diameter usually between 0.5 and 1.5 mm travelling between 2 and 4 times the speed of sound.
4
For toughest operations, including cutting hard materials such metals, a second stage is added. The supersonic jet is travelling through this stage, creates a venturi effect to mix abrasive sand. The sand is accelerated by the water, creating a highly powerful supersonic particle stream erosion (PASER® is the first patent for an abrasive waterjet cutting head in the early 80’s)
See it in Action
Waterjet is an impressive solution to view. Take a moment to browse our videos below.
High-Pressure Deburring
Downloads
Interested in reading more, take a moment to review our collection of brochures and other materials related to ultrahigh-process waterjet solutions.
Waterjet Blasting for Ceramic Shell & Core Removal
Ultrahigh-Pressure Waterjet Machining
Ultrahigh-Pressure Waterjet Stripping
Frequently Asked Questions About Waterjet
What pressure do you usually operate?
Most industrial applications runs between 1500 bar and 6000 bar. For abrasive waterjet, it is usually between 3500 bar and 6000 bar.
What is the diameter of the jet?
Typically, between 0.5 mm and 1.5mm. For some applications, multijet heads or fanjet heads can be used.
Can you cut metals?
Yes, actually metal cutting is one of the best use of waterjet. But abrasive waterjet is needed.
How thick can you cut?
Some customers did cut 500mm of stainless steel, but most industrial applications are between 0 and 300 mm.
How thin can you cut?
Virtually, there is no limitation.
Don’t you damage the base material when using so much pressure to remove a coating?
The beauty of waterjet is the combination of incredible power and soft tool. When using the right setup, you can remove hard coating such as plasma sprayed thermal barrier without damaging the base material.
Can you recycle the abrasive when using abrasive waterjet?
Abrasive is a consumable that is damaged by the cut. It is not traditionally recycled because it was not found to be economical. It is usually considered a non-hazardous mineral waste that has to be disposed accordingly.
Can you use ultra-high pressure waterjet outdoor?
Yes, lot of applications using direct drive pumps powered by a diesel engine to be transportable on site for outdoor work.
How much water is needed?
A typical jet requires a flowrate of 3 liters/min.
Can you recycle the water?
Yes, water closed-loop system is available for most applications.
What can you cut with waterjet?
Virtually any material! From food products, to automotive interiors, from gaskets to insulation materials, from non-woven to diapers, from metals to carbon fiber composites, from stone to granit, from kitchen tops to ceramic tiles, from glass to PEHD, waterjet can cut any material.
Can you cut 3D parts?
Yes, waterjet can be used to process flat plates but also 3-dimensional parts. A rule of thumb is: “If you can draw it, waterjet can cut it!”
What tolerance do you achieve with abrasive waterjet cutting?
Abrasive waterjet typical accuracy is +/- 0.2mm. With a proper set-up, it is possible to go down to +/- 0.05mm or even better.
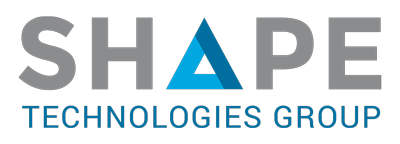
Aquarese is proud to be a Shape Technologies Group company, partnering with the world leaders in UHP technology to engineer and deliver the future of manufacturing process solutions.