Waterjet Cutting
Advanced Parts. Advanced Materials. Advanced Solutions.
Ultrahigh-Pressure Abrasive Waterjet Cutting & Machining
Waterjet is the part processing solution of the future. Quickly and accurately cut a wide variety of geometries and materials with high performance and ease. From processing advanced materials including titanium, superalloys and composites to cutting virtually any geometry with full 3D capabilities and precise tolerances, UHP waterjet cutting shapes your part to your specifications.
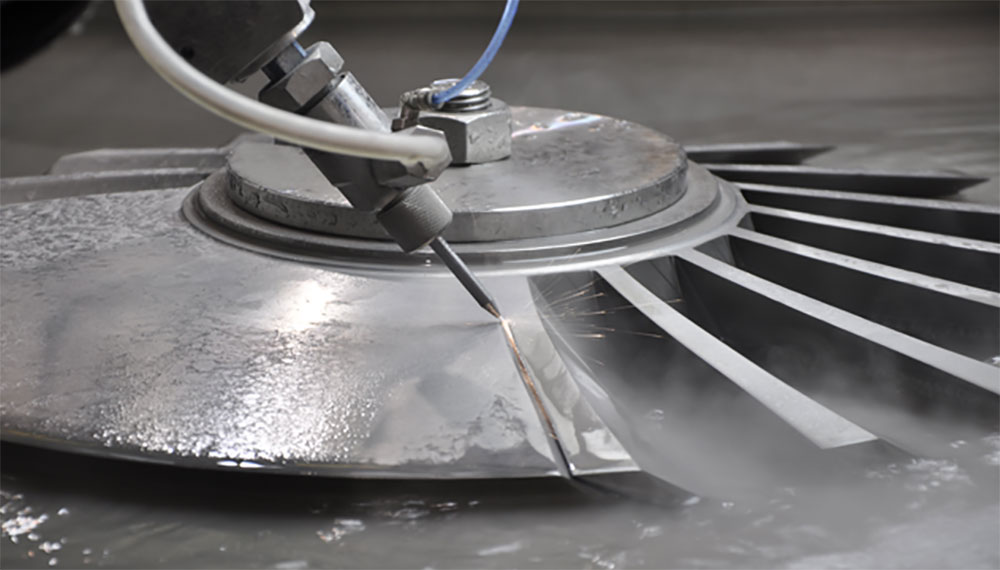
High Performance Cutting
Cut up to 10 times faster than milling with a tool life of up to 500 times longer.
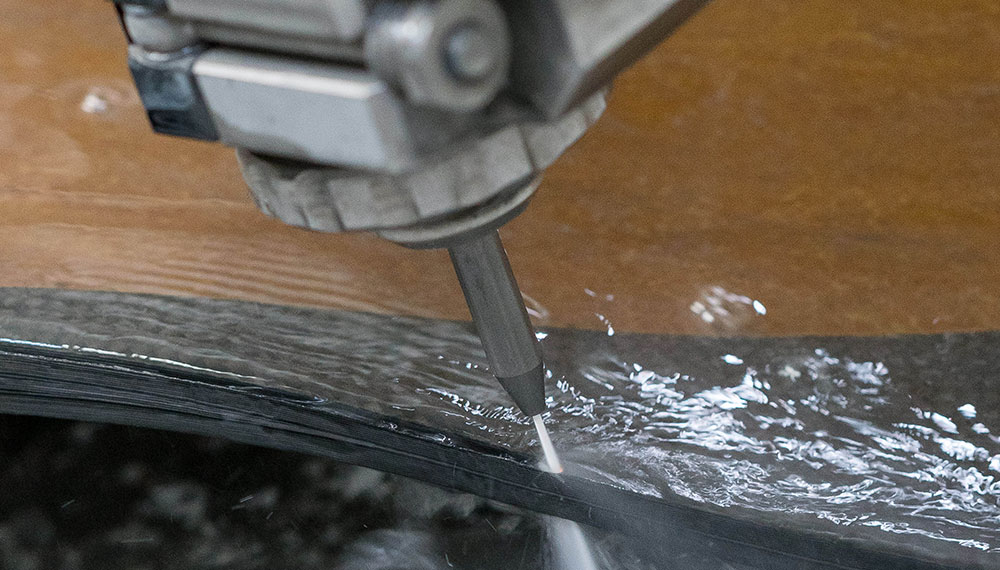
Preservation of Part Integrity
No Heat Affected Zones (HAZ) or cracking or material delamination.
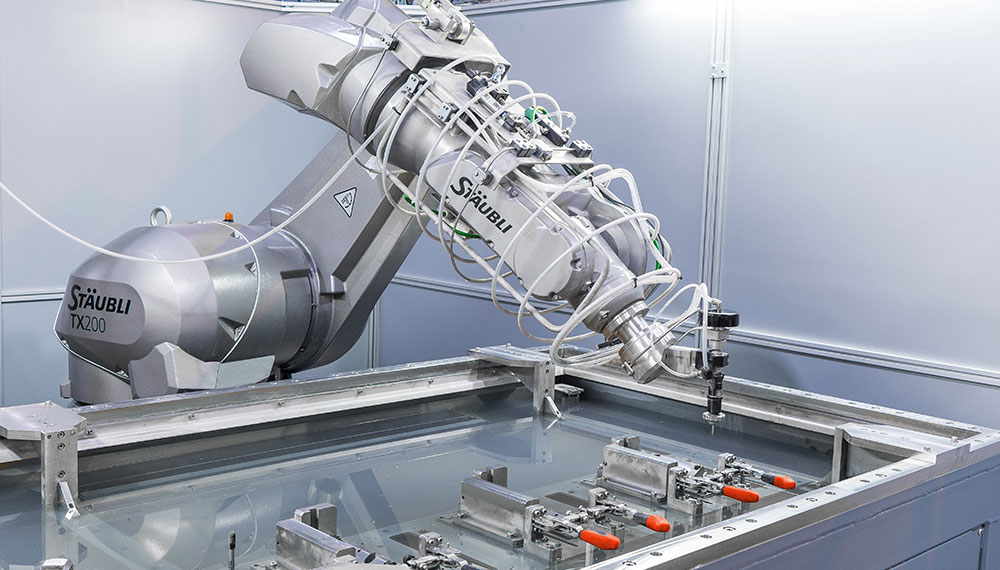
Full 3D Capabilities
+/-100° degrees of wrist movement and positional accuracies of +/- 0.1 mm. Add additional axis if required.
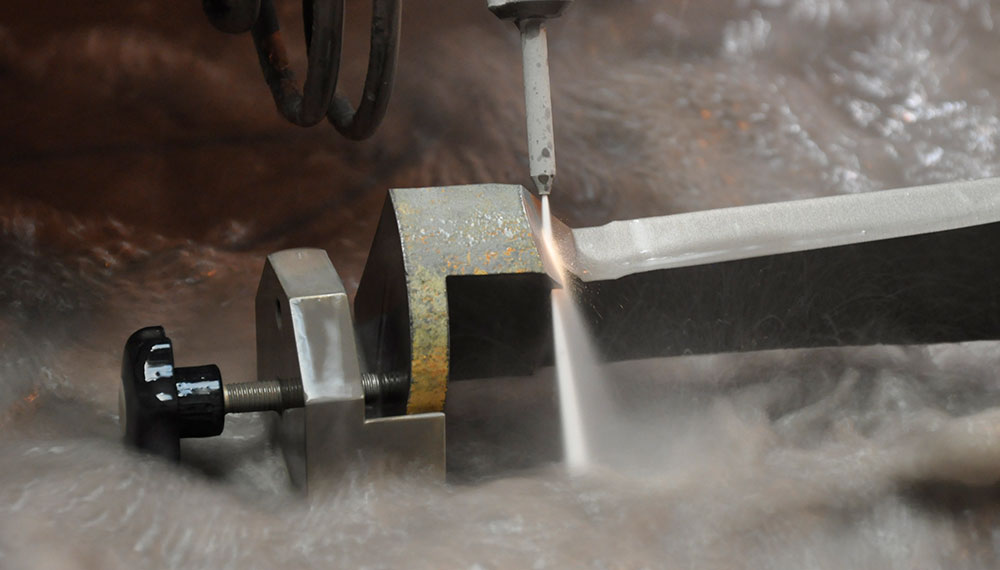
Optimal Material Utilization
3D & 2D nesting capabilities, and easy recycling of off-cuts.
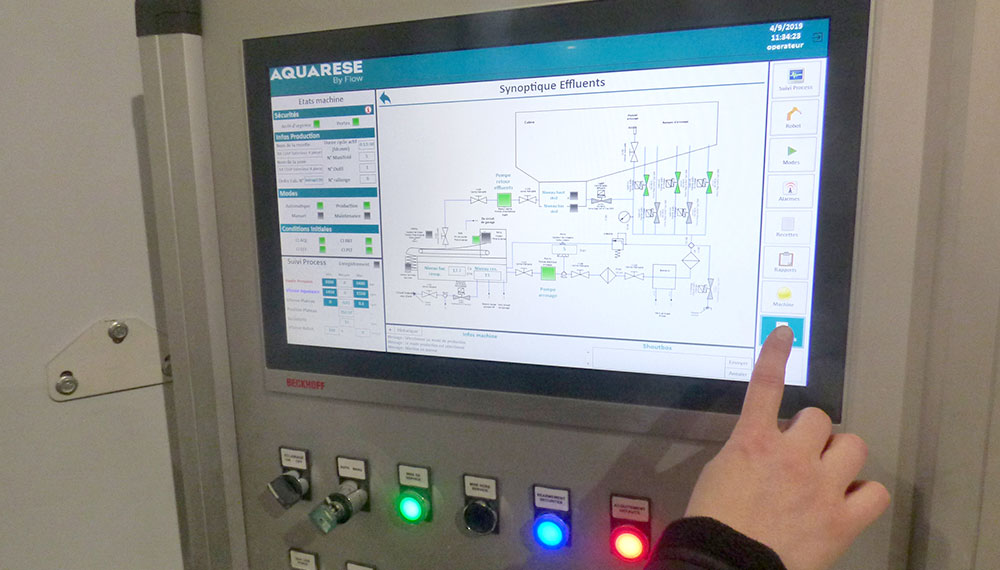
Comprehensive Process Monitoring
Guarantee the quality of your parts without human supervision, traceability reports included.
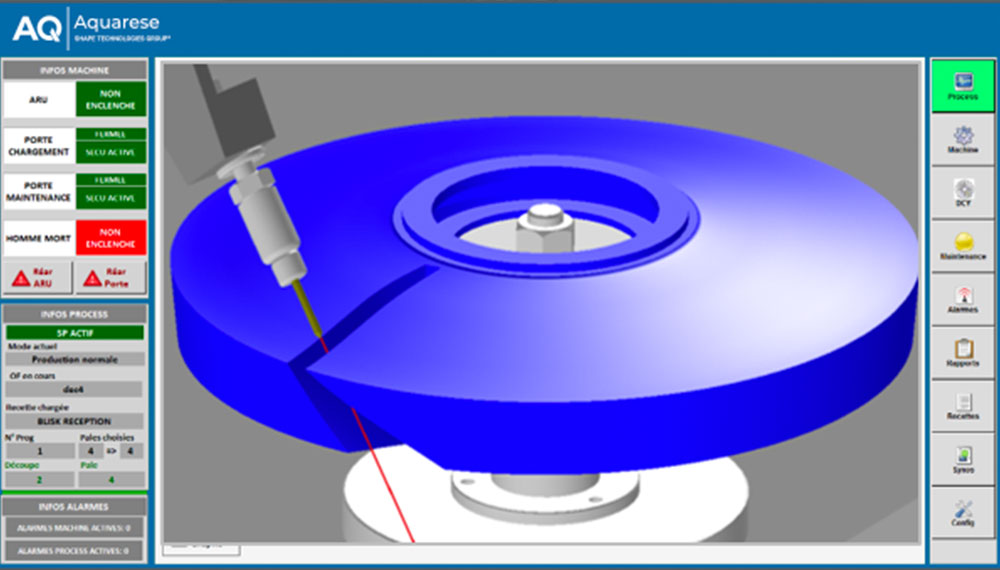
Easy Programming
User-friendly interface with job-specific functions. Waterjet CAM software for both 2D & 3D cutting.
Whether cutting turbine blades, blisks, composites structures, or other complex parts,our ultrahigh-pressure precision solutions are the ideal way to process parts.
Degating for Foundries
Objective: Separate the casted part from the tree / sprue / runner system
Waterjet cutting provides advantages in safety, material removal rates and automated operations compared to disk cutting.
Benefits:
- Simplify downstream operations: Highly repeatable cutting that allows you to cut closer to tight part geometries, including complex shapes
- Improves operator safety: No hazardous manual cutting, reduced noise levels, no dust generated
- Preserves the integrity of your parts: No Heat Affected Zone (HAZ). No stress / part deformation
- Competitive: low operating cost to cut tough materials (titanium, superalloys)
- Saves material: kerf (jet diameter) is 1.5mm / 0.06”
Levelling for Foundries
Objective: Remove runner system to get the finished part.
Waterjet safely eliminates grinding with limited operator involvement – hands off the parts.
Benefits:
- Eliminates or reduces the need for machining: get to the finished parts including those with complex geometries
- Improve safety: no dust, reduced noise level, repeatable results, hands off the part
- Preserves the integrity of your parts : parts are not bent, no stress
Trimming for Composites
Composite lay-up process parts requires a downstream trimming of the excess flashing.
Benefits:
- Follow complex 3D profiles and adapt to part variations with Adaptive WJ Machining
- High cutting efficiency: waterjet is always sharp providing a clean cut – no dust, no fiber pull out
Low fixturing cost: little effort generated by waterjet enables simpler fixtures
Deflashing for Forges
Objective: Remove flashing (also called “burr”), generated by the forging process, from the part. Waterjet safely and accurately replaces manual cutting by plasma.
Benefits:
- Cut any material in any thickness
- Highly repeatable cutting that allows you to cut close to part geometries
- Follow complex 3D part profiles
- No HAZ (Heat Affected Zone)
Improves operator safety: no hazardous manual cutting, automated operation
Rough Machining for Turbine Components Machining
Objective: remove bulk material to get near net-shape of complex turbine components (blisks, blades, etc).
Benefits:
- Improved cycle times – higher material removal rate compared to other technologies (rough milling, EDM, ECM)
- Low operating cost
- Maximize revert / recycle by generating large offcuts instead of chips
- Process any material type
- High thickness to fine geometry
Our Cutting Machine
Our waterjet solutions maximize up-time, and even automate your production lines. Continuous monitoring and archiving of process parameters ensures efficient, reliable cutting. Our waterjets are IoT ready, and easily integrate into established production.
Additionally, waterjet is an eco-friendly solution, with no hazardous waste.
Manufactured for High Production
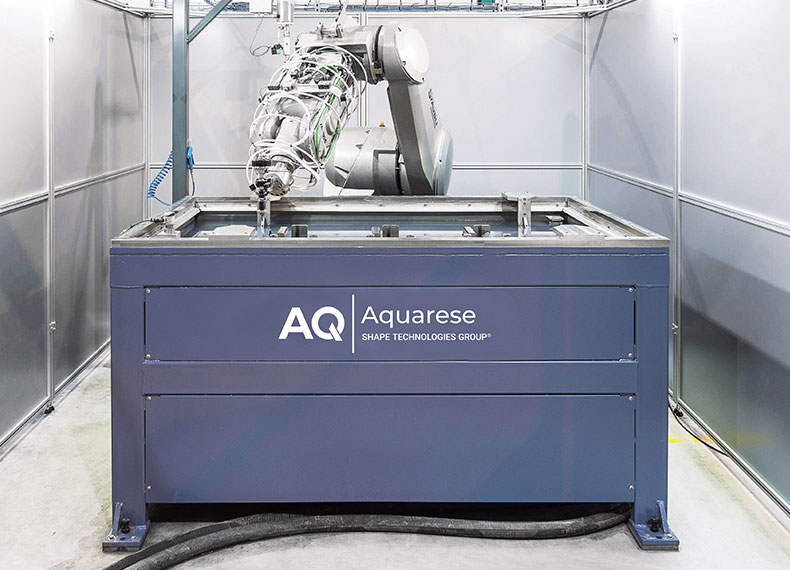
Our waterjet solutions easily integrate into manufacturing process lines including those that are IoT enabled. Designed for 24/7 operation, you can expect reliable productivity, day in and day out.
Continuous part monitoring and abrasive extraction provides maximum productivity for your operations. A soundproof enclosure (75 db, no noise, no water, no abrasive near your operator), and easy material loading make the Aquarese solutions a great addition to your production.
Aquarese waterjet solutions are used in the production of: guide vanes, motor crankcases, diffuser inserts, airfoils, turbine vanes, turbine disks, jet engine structural parts, shieldings, tools and controls, boring products, stamped parts, foundry parts, customized material batch cutting, and more
Our Team is Your Team
Our waterjet stripping experts understand what it’s like to perform waterjet stripping day in, and day out. We strip aerospace and nuclear parts for our customers every week in our Advanced Production centers. Our process know-how and everyday operation allows us to partner with our customers in a unique way. Our lifetime support means you can rely on our partnership for years to come.
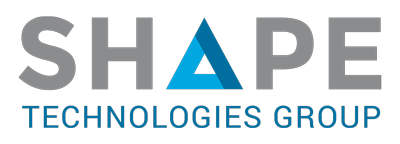
Aquarese is proud to be a Shape Technologies Group company, partnering with the world leaders in UHP technology to engineer and deliver the future of manufacturing process solutions.